GE Has 3D-Printed a Working Jet Engine
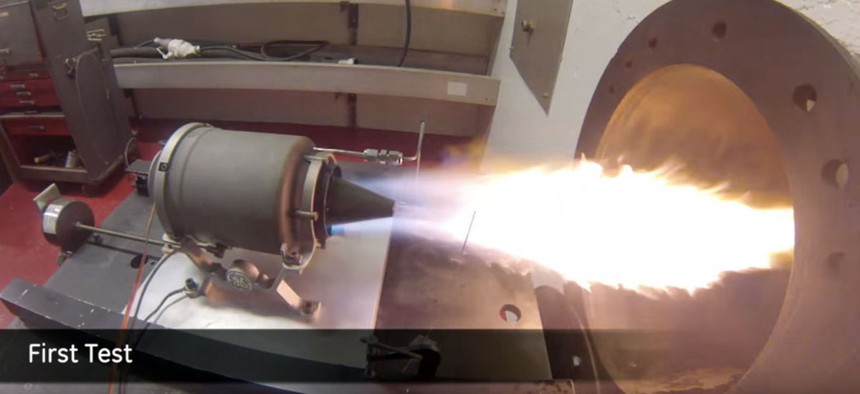
Youtube/GE Reports
While the consumer 3D printing industry is going through a bit of an existential crisis, industrial 3D printing is going strong.
While the consumer 3D printing industry is going through a bit of an existential crisis, industrial 3D printing is going strong. Last week, Stratasys announced it had 3D-printed over 1,000 parts for Airbus’ A350 XWB planes that shipped in 2014. Now, scientists at GE Aviation’s Additive Development Center have made a working jet engine entirely from 3D-printed parts.
The catch: The engine is about the size of an American football, so it’s unlikely to be installed on any commercial planes in the near future. But that doesn’t mean it can’t fly: GE says the engine made from additive processes can spin at up to 33,000 rpm, and is based on a design from a radio-controlled jet engine model plane. (Model jet planes are a big deal for some hobbyists.)

“There are really a lot of benefits to building things through additive,” Matt Benvie, a spokesman for GE Aviation said in a blog post. “You get speed because there’s less need for tooling and you go right from a model or idea to making a part. You can also get geometries that just can’t be made any other way.”

While this engine was just a small-scale side project for GE’s engineers, there is the potential for 3D printing to help develop more complex designs with less waste than traditional manufacturing techniques.