MIT Researchers 3-D-Print Customizable Padding for Robots
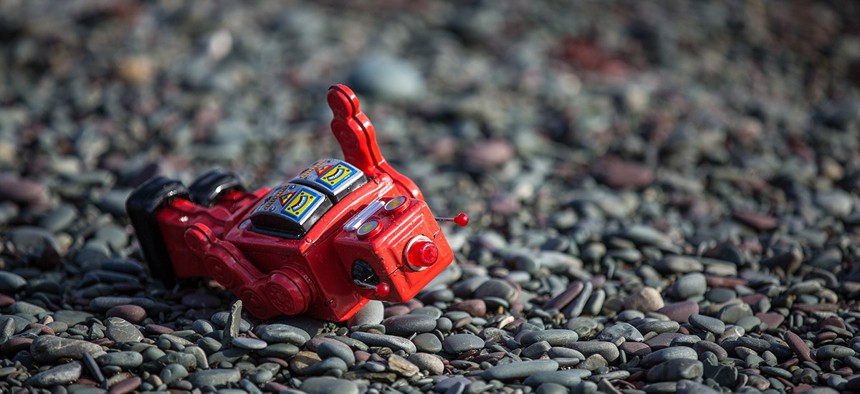
CookiesForDevo/Shutterstock.com
A wrong landing could be all it takes to break a robot.
A wrong landing could be all it takes to break a robot.
To protect our robot friends from their inevitable falls, researchers at MIT’s Computer Science and Artificial Intelligence Laboratory are creating customizable shock-absorbent padding. The team’s Programmable Viscoelastic Material technique allows users to digitally program every part of a 3-D-printed object to exact levels of stiffness and elasticity.
“We can make really effective dampers and those dampers can be tailored exactly to the application by controlling the amount of liquid and solid,” one of the researchers, Robert MacCurdy, told Quartz.
Although viscoelastics like rubber and plastic are cheap, compact and readily available, they can prove hard to customize to specific levels of damping, which can reduce the rebound after impact. With this new technology, the amount of fluid injected into the material can be controlled, with more fluid leading to more bounce.
There’s also no need to make multiple parts with varying absorbability that have to be assembled. The viscoelastic coating can be applied while 3-D printing the robot itself.
The added layer will not only protect sensitive parts like cameras and sensors, but it could also make it easier to control how the robots land.
”Our process allows you to have mechanical differences throughout the body of the robot,” co-author Jeffrey Lipton said.
Customizing the exterior of a robot using PVM makes its landing nearly four times more precise, researchers say, helping extend its lifespan.
The concept can be applied to protect other electronics like drones and phones, as well as sporting equipment such as shoes and helmets.
“You could have certain parts [of a helmet] made of materials that are comfortable for your head to rest on, and other shock-absorbing materials for the sections that are most likely to be impacted in a collision,” MacCurdy said.
Learn more in the video below: