3D Printing Has Gone Metal
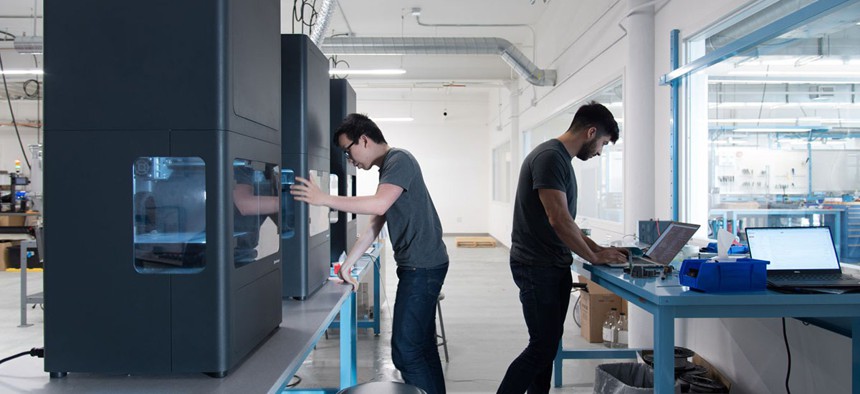
Markforged
The fourth industrial revolution may well be back on.
The fourth industrial revolution may well be back on.
3D printing startup Markforged announced today that it has secured $30 million in funding from three partners (who are also customers) that see value in using its technology to speed up the prototyping and production of their products. The round was led by Siemens’ venture arm, next47, joined by Microsoft and Porsche, which is part of the Volkswagen Group.
The promise of 3D printing has always been that anyone will eventually be able to use a magic box to make anything they need near-instantaneously, much like the Replicator machines on Star Trek. But the reality hasn’t been quite that dramatic. Consumer 3D printers have failed to take off—they’re expensive, slow, hard to use, and can only print in a small range of materials—and commercial printers aren’t faring much better. While some 3D printers (such as Carbon) have massively increased the speed at which plastic parts can be printed, and others are using multiple materials (including metals found in airplane parts), very few have successfully replaced traditional manufacturing processes. Markforged believes it can change that.
The company was founded by CEO Greg Mark five years ago, and launched with a novel method for 3D-printing carbon fiber, regarded as one of the most cost-effective ways to make durable parts that can in some instances even replace metal parts. Mark told Quartz that the company’s carbon fiber parts can be used as the fittings for factory moulds that traditionally would have been cast in metal, a considerably slower process. In January, Markforged announced a range of $100,000 commercial printers that use the same technology to print in steel.
Markforged’s approach to metal products is different than other 3D printers. The existing metal printers tend to cost between $500,000 and $1 million, and use lasers to melt metal powders into shapes, layer by layer. Markforged’s printer, on the other hand, extrudes metal powder that’s held in place by plastic, which is then dissolved, and the metal powder is sintered. It’s a similar process to how many metal parts are made today, with using the same materials found injection molding, just instead of injecting a part into place, it’s printed.
The machines print in a sort of honeycomb pattern, similar to the inside of human bones, something that takes up far less material than traditional injection molding. Mark says the end result is a metal product that’s 90% as strong and 60% lighter than a traditional piece of machined metal, with no wasted metal shavings.
Markforged’s metal prints are also strong in any direction. Many other prints might hold together in certain directions, but could shear along the plane that they were printed because the metal from each layer was heated as it was laid rather than heated together.
When Mark showed me parts made from the company’s newest printers, they felt as durable as any that had been made using traditional methods. He handed me a brake lever for a Ducati motorbike (printed for his own bike), as well as metal nuts and bolts that were printed together. In both cases, it was difficult to tell that the parts had been printed rather than injection-molded.
Mark ultimately hopes to make commercial 3D printing as useful and easy as spinning up a new server is for an internet startup, and the latest round of funding will be geared at scaling up production so that the company can offer what he calls “full-stack printing” to any customer by the end of 2018. To achieve that goal, Mark says he looked beyond VCs vying for quick returns, and instead at those investing in companies that want to change how tomorrow’s goods are produced.
At maximum capacity, Mark says his system is able to network together thousands of printers making identical metal products, and is roughly 50 times faster and 20 times cheaper than machining those same parts would be. This could be a massive boon for the next generation of Microsoft Surfaces, Porsches, or Siemens wind turbines, and how long it takes to produce them.
So far, Markforged has struggled to realize its grand vision—it’s too busy selling printers faster than it can make them—but the latest funds could help the company move forward with its more ambitious plans. Whether this will be the push the industry needs to realize the dream of 3D printing for more than making tchotchkes is unclear. But it definitely shows what could be possible when we think about creating products the same way we do building apps.