Army Research Shows How Do-It-Yourself Facemasks Can Be as Safe as N95s
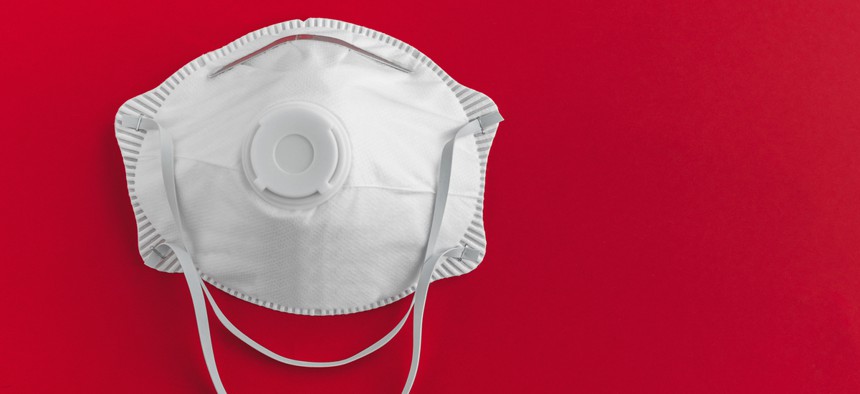
Antonio Rico/Shutterstock.com
Personal protective equipment for hospital workers is running out. This design works as well as the best in class.
Shortages of facemasks have many people making their own — not just grocery shoppers and Pentagon staff, but even medical professionals in coronavirus-wracked hospitals. Scientists with the Army Research Lab, working with a Massachusetts hospital, have figured out the best easy-to-find materials for making homemade masks: a layer of absorbent cloth combined with a water-repelling fabric, preferably one treated with Scotchgard.
At the end of March, Dr. Michael Rosenblatt, chief medical officer at Lahey Hospital in Burlington, Massachusetts, contacted the Army with an urgent need. The lack of PPE was so severe that surgeons at his hospital had to use the same surgical masks for an entire day or longer.
“I can’t put in words the stress we have on PPE,” Rosenblatt told Defense One. “We are relying on technology to recycle PPE right now, some of which is unproven, some of which is recently proven, but the logistics in terms of turning these N95 masks around is really questionable,” he said. “Maximally, everyone should be in respirators. But there aren’t enough respirators to go around. So now we’re in surgical masks. We’re burning through the surgical masks.”
He wanted help to develop a mask that had “some science behind the selection of materials that would create a mask that would be as good as an N95 mask or better.”
Steven Lustig, an associate professor at Northeastern University and a chemical engineer at the Army Research Lab, gathered a small team of students and set out to help.
They engineered a nanoparticle that was the same size and character as COVID-19, but fluorescent, so you can see it with a special microscope. They then took two milliliters of the nanoparticle solution — the equivalent of about two dozen sneezes in water droplets — and put it into an artist’s airbrush. The air leaving the airbrush creates an aerosol that’s passed through the test material. On the other side of that is a glass slide to pick up any particles that made it through. Using a fluorescent microscope and an algorithm, you can count the nanoparticles on the glass and then compare that to the number of particles that would have gone through without any material or with N95 or other medical masks that have already met rigorous standards set by the American Society of Testing and Materials.
“We really calibrated our technique based on masks that had already been certified,” said Lustig. So far, he reports that they’ve found nine designs that are statistically equivalent to N95 masks — and two that are better.
The ideal made-at-home masks need an absorbent layer composed of something like quilted cotton, terrycloth, dense flannel, a heavy T-shirt, etc. You also need at least one layer that’s hydrophobic, meaning that it repels water, such as a polyester fabric like OLY-Fun, preferably treated with Scotchgard. The more layers you add, alternating back and forth, the better you are protected.
“The real issue here is knowing designs that are good enough and what to stay away from,” he said.
The materials for Lustig’s research were provided by Jo-Ann Stores.
“Using a lot of common-sense everyday materials to say, hey, what’s a hell of a lot better than nothing?” said Wade Miquelon, the company’s president and CEO. “Given the size of this debacle, [that’s one of] one of the simplest, smartest best ways to slow things down. I just feel you can spend trillions of dollars doing other things, but with this kind of common sense and very quick agility and speed, for policymakers to be able to support it…makes a whole lot more sense and bang for buck than anything else you can do right now.”
The Army’s Combat Capabilities Development Command, or CCDC, is also developing prototype masks for soldiers. While Lustig’s efforts might not make it into the prototype that CDCC ultimately decides on, a CCDC official confirmed to Defense One that the research was part of a broader effort to get a new mask to frontline soldiers quickly.
The researchers will publish their findings later this month.